芯片產(chǎn)業(yè)鏈系列7半導(dǎo)體設(shè)備-晶圓加工設(shè)備
上一篇文章中我們已經(jīng)對半導(dǎo)體設(shè)備的全景做了一次鳥瞰,并且針對硅片制造設(shè)備進(jìn)行了簡單梳理?,F(xiàn)在我們將目光轉(zhuǎn)向半導(dǎo)體設(shè)備的第二個領(lǐng)域,即晶圓加工設(shè)備,讓我們一起出發(fā)吧。
我們已經(jīng)知道晶圓加工工序分別是氧化—光刻—刻蝕—拋光—摻雜和 CVD 沉積/PVD沉積—晶圓中測,主要涉及到的生產(chǎn)設(shè)備分別是氧化爐(熱處理設(shè)備之一)、光刻機(jī)、刻蝕機(jī)、 CMP 拋光機(jī)、離子注入機(jī)、薄膜沉積設(shè)備、清洗機(jī)和檢測機(jī)等。
1、熱處理設(shè)備:熱處理工藝主要應(yīng)用的熱處理工藝主要有:氧化、擴(kuò)散、退火、合金,所使用到的半導(dǎo)體設(shè)備有氧化爐(又分為臥式爐和立式爐)、快速熱處理(RTP,Rapid Thermal Processing)設(shè)備等。半導(dǎo)體制備過程所處的超凈間寸土寸金,目前更節(jié)約空間的立式爐已逐步替代臥式爐;不同于臥式爐、立式爐的批量處理方式, RTP 采用的是單片熱處理方式。
? ? ? ? ?
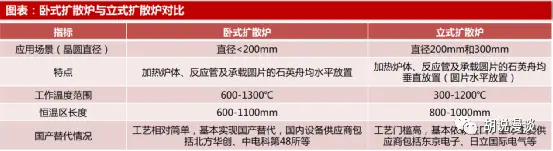
幾種熱處理工藝簡單介紹如下:氧化(Oxidation)是指加入氧氣在晶圓表面反應(yīng)生產(chǎn)一層二氧化硅,從而實(shí)現(xiàn)表面鈍化、絕緣及防止摻雜物進(jìn)入硅面的效果。擴(kuò)散(Diffusion)是實(shí)現(xiàn)摻雜工藝的方法之一,指利用熱擴(kuò)散原理,使雜質(zhì)元素在高溫的作用下?lián)饺牍枰r底中,實(shí)現(xiàn)工藝要求的濃度分布,用于制作PN結(jié)或構(gòu)成集成電路中的電阻、電容、互連布線、二極管和晶體管等器件,目前離子注入已逐步取代擴(kuò)散成為了主流的摻雜方法。退火(Anneal)是指通過加熱使晶圓產(chǎn)生特定的物理、化學(xué)變化,并在晶圓表面增加或移除少量物質(zhì),實(shí)現(xiàn)消除晶格缺陷和消除硅結(jié)構(gòu)晶格損傷的目的,常用于離子注入工藝之后。合金(Alloy)則是將硅片放置在惰性氣體環(huán)境中進(jìn)行低溫?zé)崽幚恚菇饘伲ˋl/Cu)和硅基形成良好的基礎(chǔ),穩(wěn)定Cu配線的結(jié)晶結(jié)構(gòu)并去除雜質(zhì),從而提高配線的可靠性。
? ? ? ? ?
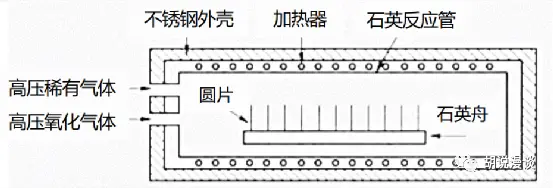
? ? ? ? ?
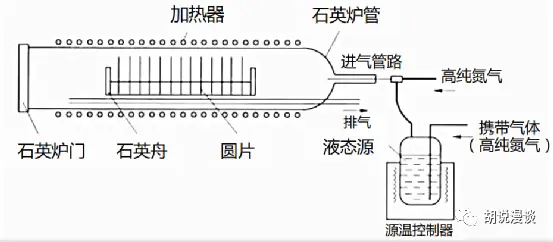
? ? ? ? ?
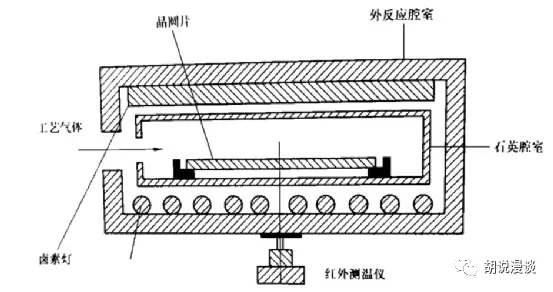
從熱處理技術(shù)的發(fā)展來看,集成電路行業(yè)的快速發(fā)展對熱處理技術(shù)提出的要求越來越高,于是,快速熱退火技術(shù)(RTP)在半導(dǎo)體制造中的競爭優(yōu)勢愈發(fā)明顯:普通爐管退火設(shè)備加熱時長需幾小時,而快速熱退火設(shè)備只需幾秒甚至幾毫秒,可有效降低總體熱預(yù)算。熱處理設(shè)備合計(jì)占半導(dǎo)體制造設(shè)備份額約3%。根據(jù)Gartner數(shù)據(jù),2020年全球半導(dǎo)體熱處理設(shè)備市場規(guī)模為15.4億美元, 其中RTP設(shè)備市場規(guī)模為7.2億美元,氧化/擴(kuò)散設(shè)備市場規(guī)模約5.5億美元, 柵極堆疊(Gate Stack)設(shè)備市場規(guī)模為2.7億美元。2025年熱處理設(shè)備市場規(guī)模有望達(dá)到19.9億美元。
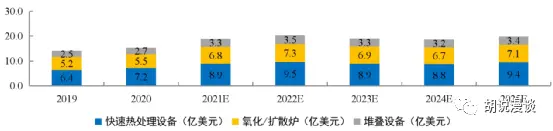
從競爭格局來看,目前,Applied Materials、Tokyo Electron、Kokusai三家海外企業(yè)占據(jù)全球熱處理設(shè)備市場絕大多數(shù)份額,三者市占率合計(jì)約80%,其中 Applied Materials單家的市場占有率更是達(dá)到了40%。在全球快速熱處理市場,2020年Applied Materials以70%的市占率位列第一,屹唐股份(Mattson)以11%的市占率位列第二,另外3家主要的廠商分別為Hitachi、Veeco以及Screen,前 5 大廠商幾乎占據(jù)了全球快速熱處理設(shè)備市場的全部份額。國內(nèi)主要熱處理設(shè)備的生產(chǎn)廠商有北方華創(chuàng)、屹唐股份,北方華創(chuàng)的立式爐/臥式爐達(dá)到國產(chǎn)半導(dǎo)體設(shè)備領(lǐng)先水平,屹唐股份在2016年收購以RTP為主導(dǎo)產(chǎn)品的Mattson后已有設(shè)備進(jìn)入了5nm邏輯芯片量產(chǎn)產(chǎn)線。華卓精科也具有UPEALA-200/300系列熱處理設(shè)備。
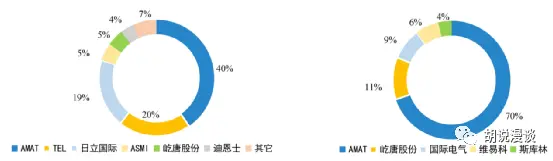
2、光刻機(jī):光刻機(jī)是光刻工藝的核心設(shè)備,被譽(yù)為半導(dǎo)體工業(yè)皇冠上的明珠,其原理為光復(fù)印工藝經(jīng)曝光系統(tǒng)用投影方法將掩模上的大規(guī)模集成電路器件的結(jié)構(gòu)圖形畫在涂有光刻膠的硅片上,經(jīng)物鏡補(bǔ)償?shù)裙鈱W(xué)誤差,通過光的照射映射到晶圓上,生成電路圖。
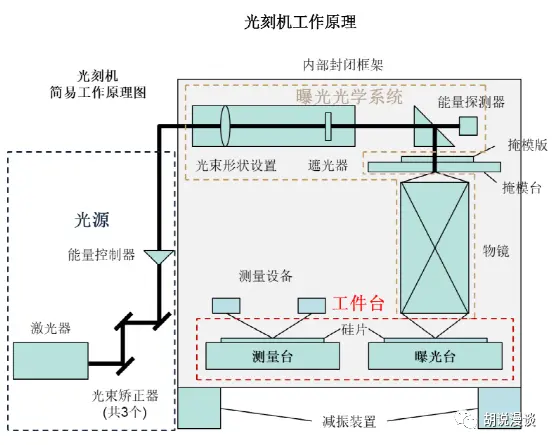
光刻機(jī)是所有半導(dǎo)體制造設(shè)備中技術(shù)含量最高的設(shè)備,包含上萬個零部件,集合了數(shù)學(xué)、光學(xué)、流體力學(xué)、高分子物理與化學(xué)、表面物理與化學(xué)、精密儀器、機(jī)械、自動化、軟件、圖像識別領(lǐng)域等多項(xiàng)頂尖技術(shù)。光源是光刻機(jī)的核心零部件之一,一般而言,光刻系統(tǒng)能獲得的分辨率越高,則成品所能獲得的最小尺寸越小, 這需要減小照射光源的波長,光源波長越短,光刻機(jī)分辨率越高,制程工藝越先進(jìn)。根據(jù)光源波長不同,市面上主流的光刻機(jī)可分為g-line、i-line、KrF、ArF、EUV五種,每次光源的改進(jìn)都顯著提升了光刻機(jī)的工藝水平、生產(chǎn)效率、良率。
五代光刻機(jī)的主要差異是光刻機(jī)的工藝節(jié)點(diǎn),即限制成品所能獲得的最小尺寸,目前第五代EUV光刻機(jī)的最小工藝節(jié)點(diǎn)達(dá)到了最優(yōu)。在光刻機(jī)的更新迭代中,對光源、 光學(xué)透鏡、反射鏡系統(tǒng)也提出了越來越高的要求。第一代的g-line光刻機(jī)逐漸走向邊緣,我們簡要介紹下其他四代光刻機(jī)。
第二代i-line 光刻機(jī):光源方面,使用波長為365nm的紫外光作為光源,通常采用汞燈或氙燈。曝光方面,i-line光刻機(jī)往往采用接觸式曝光(將掩模與光刻膠直接接觸,可能導(dǎo)致掩模和光刻膠之間的污染和損傷, 降低掩模的使用壽命)。應(yīng)用方面,盡管i-line光刻技術(shù)已經(jīng)被深紫外光刻技術(shù)所替代,但在針對部分舊款半導(dǎo)體工藝和制造流程、MEMS(微機(jī)電系統(tǒng))制造、顯示器制造、大型光掩模上仍然需要使用i-line光刻機(jī)。
第三代KrF光刻機(jī):全稱為Krypton Fluoride Excimer Laser Lithography。光源方面采用波長為248nm的深紫外線光源,即使用氪氟準(zhǔn)分子激光,比i-line光刻機(jī)具有更高的分辨率和更小的制程 。曝光方面,KrF光刻采用掃描投影式(Scanning Projection Exposure)曝光方式,光源通過鏡頭和掩模進(jìn)行投影,將電路圖案投影到電路板上,通過將掩模和光刻膠之間的距離控制在納米級別來進(jìn)行曝光,避免了接觸式曝光中可能導(dǎo)致的污染和損傷。應(yīng)用方面,KrF光刻機(jī)在制造高密度DRAM、SRAM、閃存等存儲器件時表現(xiàn)出色。
第四代ArF光刻機(jī):全稱為Argon Fluoride Excimer Laser Lithography。光源方面采用波長更短的193nm的深紫外線光源,即氬氟準(zhǔn)分子激光。ArF光刻機(jī)有兩種類型,分別是 ArF immersio(浸沒式 DUV)和 ArF dry(干式 DUV)。ArF immersio采用液體浸沒技術(shù),在曝光過程中,將掩模和硅片之間涂上一層液體介質(zhì),可以提高曝光分辨率和制程能力。ArFdry相對于液浸技術(shù)更加簡單和穩(wěn)定。在曝光過程中,不需要使用液體介質(zhì),可以直接進(jìn)行曝光,但制程能力相對于ArF immersio稍差。KrF光刻機(jī)主要集中在高端芯片市場,如制造高性能計(jì)算機(jī)、云計(jì)算、人工智能等領(lǐng)域所需的芯片。
第五代EUV 光刻機(jī):全稱為極紫外光刻(Extreme Ultraviolet Lithography),是目前最先進(jìn)的光刻技術(shù)之一,可以用于10nm以下的先進(jìn)制程。光源方面使用波長為13.5nm的極紫外光,即采用鍺(Ge)和錫(Sn)混合的等離子體光源,產(chǎn)生高能量的光子來進(jìn)行曝光。曝光方面,EUV光刻機(jī)采用反射式光學(xué)系統(tǒng),曝光光線從光源進(jìn)入光刻機(jī),經(jīng)過多個反射鏡進(jìn)行光路調(diào)節(jié),最后通過掩模進(jìn)行投影曝光。EUV光刻機(jī)可以實(shí)現(xiàn)單層掩模曝光,避免了傳統(tǒng)光刻機(jī)需要多次曝光的缺點(diǎn),大大提高了生產(chǎn)效率。同時,由于曝光光線需要穿過多層反射鏡,EUV光刻機(jī)對光學(xué)鏡片的精度和質(zhì)量要求非常高,也成了其生產(chǎn)和維護(hù)的難點(diǎn)之一。應(yīng)用方面,EUV光刻機(jī)主要用于制造10納米及以下的高端芯片。
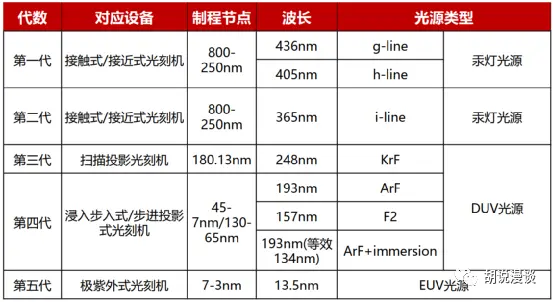
2022年全球光刻機(jī)市場規(guī)模為196億美元,同增26%。從2022年出貨量結(jié)構(gòu)來看,KrF光刻機(jī)占據(jù)大頭、出貨量達(dá)209臺。i-line光刻機(jī)次之,出貨量達(dá)185臺。受限于產(chǎn)能,EUV光刻機(jī)出貨量較低、僅40臺。從成長性來看,KrF光刻機(jī)、i-line光刻機(jī)、EUV光刻機(jī)成長性最佳,2019-2022年出貨量CAGR達(dá)27%、22%、15%,ArF 出貨量保持平穩(wěn)。從銷售額來看, 2022 年EUV銷售金額達(dá)70億歐元、占全球光刻機(jī)市場規(guī)模的36%。EUV光刻機(jī)平均售價(jià)達(dá)1.8億歐元、且一路攀升。KrF光刻機(jī)、i-line光刻機(jī)售價(jià)為411、394萬歐元。
目前全球光刻機(jī)主要市場被ASML(荷蘭阿斯麥) 、Canon(日本佳能)和 Nikon(日本尼康)三家供應(yīng)商包攬,尤其高端光刻機(jī)被荷蘭ASML廠商所壟斷,ASML在EUV領(lǐng)域占比高達(dá) 100%。我國上海微電子在90nm、110nm、280nm實(shí)現(xiàn)光刻機(jī)國產(chǎn)化,成功交付首臺2.5D\3D先進(jìn)封裝光刻機(jī),并預(yù)計(jì)在2023年年底向市場交付國產(chǎn)的第一臺28nm光刻機(jī)設(shè)備。
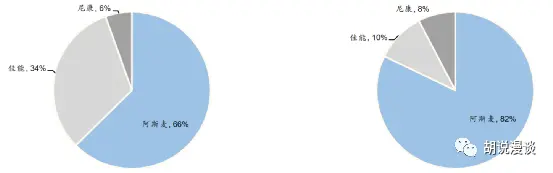
3、涂膠顯影設(shè)備:涂膠顯影設(shè)備是光刻工序中與光刻機(jī)配套使用的涂膠、烘烤及顯影設(shè)備,包括涂膠機(jī)、噴膠機(jī)和顯影機(jī)。涂膠顯影機(jī)作為光刻機(jī)的輸入(曝光前光刻膠涂覆)和輸出(曝光后圖形的顯影),工藝過程主要是通過機(jī)械手使晶圓在各系統(tǒng)之間傳輸和處理,完成晶圓的光刻膠涂覆、固化、顯影、堅(jiān)膜等工藝過程。該設(shè)備決定光刻工序細(xì)微曝光圖案的形成,以及后續(xù)蝕刻和離子注入等工藝中圖形轉(zhuǎn)移的結(jié)果,是集成電路制造過程中不可或缺的關(guān)鍵工藝步驟。
涂膠顯影設(shè)備可以應(yīng)用于集成電路制造前道晶圓加工領(lǐng)域,以及后道先進(jìn)封裝領(lǐng)域,前道涂膠顯影設(shè)備:包括PI、Barc、SOC、SOD、I-line、KrF、KrFi、ArF、ArFi等工藝,后道涂膠顯影設(shè)備則用于Bumping制備工藝、WLCSP封裝工藝、Fanout封裝工藝等領(lǐng)域的光刻工序。
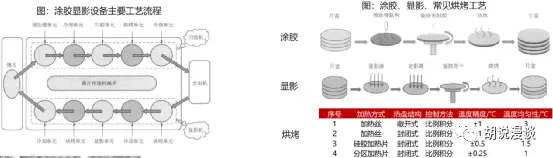
根據(jù)是否與光刻機(jī)聯(lián)機(jī)作業(yè),涂膠顯影機(jī)分為Offline設(shè)備和Inline設(shè)備。Offline設(shè)備不與光刻機(jī)聯(lián)機(jī)作業(yè),主要包括前道Barc(抗反射層)涂膠機(jī)、PI涂膠顯影機(jī)。Inline設(shè)備與光刻機(jī)聯(lián)機(jī)作業(yè),按照G-line→I-line→KrF→ArF→ArFi(浸沒式)→EUV的工藝發(fā)展路線進(jìn)行演進(jìn)。早期或較低端集成電路工藝中,主要使用獨(dú)立機(jī)臺Off-line設(shè)備,隨著集成電路工藝的提升,目前200mm及以上的生產(chǎn)線大多采用In-line設(shè)備,與光刻機(jī)配合工作。
2021年全球涂膠顯影機(jī)市場規(guī)模37億美元,其中東京電子占據(jù)絕對壟斷,全球市占率達(dá)89%。此外競爭者還有日本迪恩士、韓國細(xì)美事、德國蘇斯微(SUSS)、臺灣億力鑫(ELS)、韓國CND等。芯源微為目前國內(nèi)唯一可提供量產(chǎn)型前道涂膠顯影機(jī)的設(shè)備商,已全面覆蓋offline、KrF、ArF、浸沒式等28nm工藝節(jié)點(diǎn)設(shè)備。
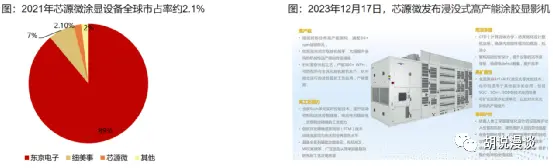
4、刻蝕設(shè)備:刻蝕工藝是利用化學(xué)或者物理的方法將晶圓表面附著的不必要的材質(zhì)進(jìn)行去除的過程??涛g工藝按原理可分為干法刻蝕和濕法刻蝕,按刻蝕材料可分為介質(zhì)刻蝕、硅刻蝕、金屬刻蝕。
干法刻蝕是指利用等離子體或高能離子束轟擊的方式來去除物質(zhì)的工藝。由于在刻蝕中不使用液體,所以稱為干法刻蝕。干法刻蝕按工作機(jī)制分為三類:物理刻蝕、化學(xué)刻蝕、物理化學(xué)刻蝕,按等離子體或高能離子束產(chǎn)生的物理機(jī)制又可分為CCP(Capacitively Coupled Plasma,電容耦合等離子體刻蝕)和ICP(Inductively Coupled Plasma,電感耦合等離子體刻蝕)。濕法刻蝕是較為原始的刻蝕技術(shù),利用溶液與薄膜的化學(xué)反應(yīng)去除薄膜未被保護(hù)掩模覆蓋的部分,從而達(dá)到刻蝕的目的。濕法刻蝕可進(jìn)一步分為化學(xué)刻蝕和電解刻蝕。
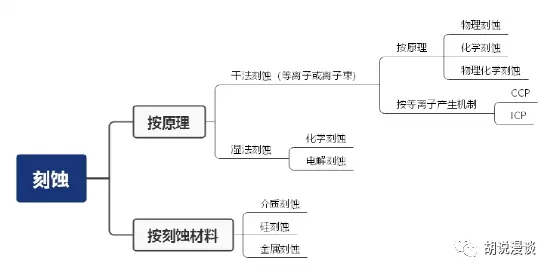
接下來我們主要的刻蝕分類進(jìn)行簡單介紹。由于濕法刻蝕的原理比較簡單,也比較顧名思義,因此我們主要通過干法刻蝕和刻蝕材料兩個角度進(jìn)行介紹。
(1)干法刻蝕中的物理刻蝕又稱濺射刻蝕或離子束銑蝕,是指刻蝕設(shè)備利用輝光放電將惰性氣體(如Ar)電離成等離子體,包含帶正電的離子和自由電子,在外加電場的作用下加速帶電離子,并轟擊在被刻蝕物表面,將被刻蝕物的原子擊出——濺射,從而完成刻蝕。該過程完全是純物理上的能量轉(zhuǎn)移,不存在化學(xué)反應(yīng)過程,故稱物理性刻蝕。其特點(diǎn)是具有非常好的方向性,可獲得接近垂直的刻蝕輪廓。但是由于離子是全面均勻地濺射在芯片上,光刻膠和被刻蝕材料同時被刻蝕,造成刻蝕選擇比差。同時,被擊出的物質(zhì)大多為不易揮發(fā)的物質(zhì),這些物質(zhì)容易二次沉積在被刻蝕薄膜的表面及側(cè)壁。因此,在超大規(guī)模集成電路制作工藝中,很少使用完全物理方式的干法刻蝕方法。
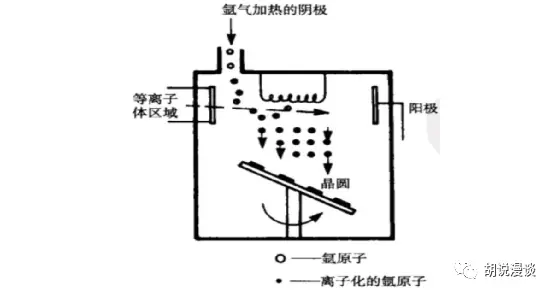
(2)干法刻蝕中的化學(xué)刻蝕又稱稱為等離子體刻蝕(Plasma Etching,PE),是指在低壓氣體環(huán)境下,刻蝕設(shè)備利用外電場將刻蝕氣體(如氯或氟氣體等)電離成等離子體,等離子體中含有自由電子、帶電離子、分子及反應(yīng)活性很強(qiáng)的基團(tuán),它們擴(kuò)散到被刻蝕薄膜表面后與薄膜表面原子反應(yīng)生成具有揮發(fā)性的反應(yīng)產(chǎn)物,并被真空設(shè)備抽離反應(yīng)腔。因這種反應(yīng)完全利用化學(xué)反應(yīng),故稱為化學(xué)性刻蝕。這種刻蝕方式與濕法刻蝕類似,只是反應(yīng)物與產(chǎn)物的狀態(tài)從液態(tài)改為氣態(tài),并以等離子體來加快反應(yīng)速率。其特點(diǎn)是具有與濕法刻蝕類似的優(yōu)點(diǎn)與缺點(diǎn),即具有高選擇比、各向同性的刻蝕特點(diǎn)。由于各向刻蝕同性,化學(xué)性干法刻蝕對于1um以下的細(xì)線條線寬損失明顯,在半導(dǎo)體工藝中,通常用在不需圖形轉(zhuǎn)移的步驟中(如光刻膠的去除)。
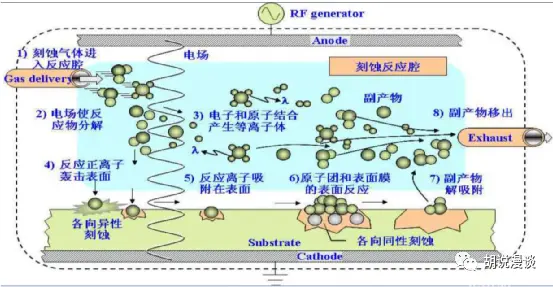
(3)干法刻蝕中的物理化學(xué)刻蝕又稱反應(yīng)離子刻蝕(Reactive Ion Etching,RIE),是指目前采用最多的刻蝕方法是結(jié)合物理性的離子轟擊與化學(xué)反應(yīng)的刻蝕。為了實(shí)現(xiàn)物理、化學(xué)兩種刻蝕方法的優(yōu)勢互補(bǔ),它將被刻蝕物放置在功率電極上,能夠使帶電離子加速轟擊刻蝕物表面,同時電離的活性離子又參與化學(xué)反應(yīng),這種方式兼具各向異性刻蝕與高選擇比刻蝕的雙重優(yōu)點(diǎn)。實(shí)際刻蝕的進(jìn)行主要靠化學(xué)反應(yīng)來實(shí)現(xiàn),加入離子轟擊的作用主要是為了破壞被刻蝕材質(zhì)表面的化學(xué)鍵以提高反應(yīng)速率,以及將二次沉積在被刻蝕薄膜表面的產(chǎn)物或聚合物打掉,以使被刻蝕表面能充分與刻蝕氣體接觸。
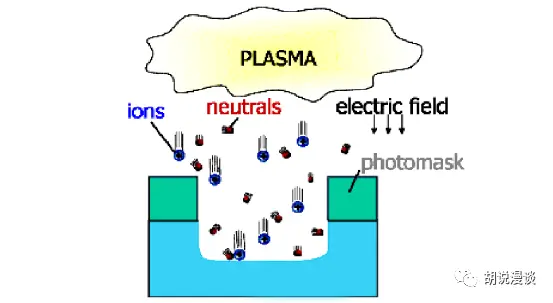
? ? ? ? ?
此外濕法刻蝕在小尺寸及復(fù)雜結(jié)構(gòu)應(yīng)用中具有局限性,目前主要用于干法刻蝕后殘留物的清洗。將以上介紹的刻蝕方法的各種特點(diǎn)和應(yīng)用范圍可總結(jié)如下:
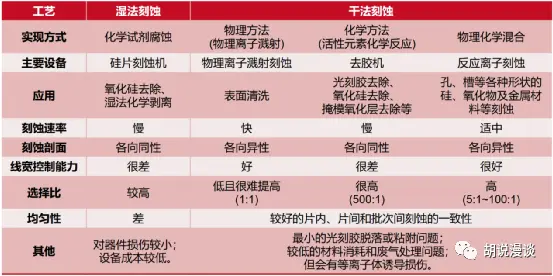
在此我們有必要介紹一下干法刻蝕中的CCP和ICP。CCP 刻蝕機(jī)利用電容耦合產(chǎn)生等離子體,這種等離子密度較低,但能量較高,適合刻蝕氧化物、氮氧化物等較硬介質(zhì)材料和掩膜等,即適用于介質(zhì)刻蝕。ICP 刻蝕機(jī)則利用電感耦合產(chǎn)生等離子體,這種等離子密度高,能量較低,但調(diào)控起來更靈活,可獨(dú)立控制離子密度和能量,適合刻蝕單晶硅、多晶硅、金屬等硬度不高或比較薄的材料,即適用于硅刻蝕和金屬刻蝕。
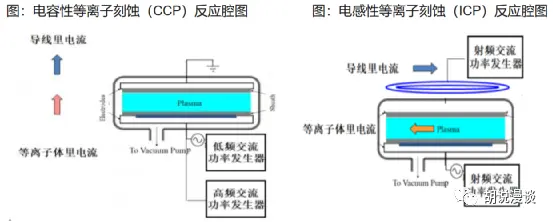
從應(yīng)用材料的角度來看,介質(zhì)刻蝕主要用于制作接觸孔,通孔, 凹槽;硅刻蝕主要用于制作柵極和器件隔離溝槽;金屬刻蝕主要用于金屬互連線鋁合金刻蝕,制作鎢塞等。
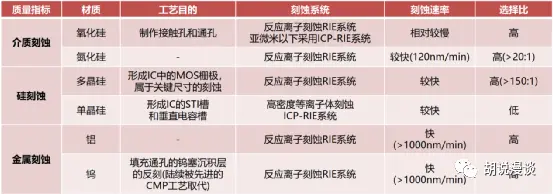
從市場規(guī)模來看,據(jù)Gartner統(tǒng)計(jì),2022年全球刻蝕設(shè)備共計(jì)約230億美元市場規(guī)模。80年代以后,隨著集成電路制程的升級,及芯片結(jié)構(gòu)尺寸的不斷縮小,濕法刻蝕在線寬控制,刻蝕方向性方面的局限性漸漸顯現(xiàn),并逐步被干法刻蝕取代,目前干法刻蝕市場占比90%以上。此外,金屬刻蝕主要是互連線及多層金屬布線的刻蝕,但隨著180nm節(jié)點(diǎn)開始,銅互連技術(shù)逐步取代鋁互連,金屬刻蝕應(yīng)用規(guī)??焖傧陆担壳皟H占比3%左右。金屬刻蝕的應(yīng)用下滑以及大馬士革工藝的運(yùn)用,也導(dǎo)致了CCP占比的提升。目前各類設(shè)備的占比如下:
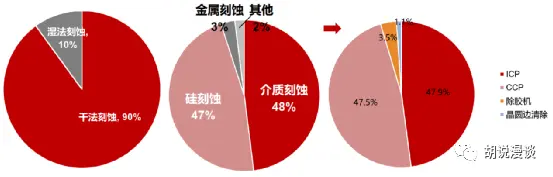
從競爭格局來看,全球刻蝕設(shè)備市場呈現(xiàn)美國和日本壟斷格局,泛林、東京電子和應(yīng)用材料全球市占率分別為46%、29%、16%。中微公司、北方華創(chuàng)的刻蝕設(shè)備處于國內(nèi)領(lǐng)先地位,部分技術(shù)水平和應(yīng)用領(lǐng)域已達(dá)國際同類產(chǎn)品標(biāo)準(zhǔn),2021年全球市占率均約2%。
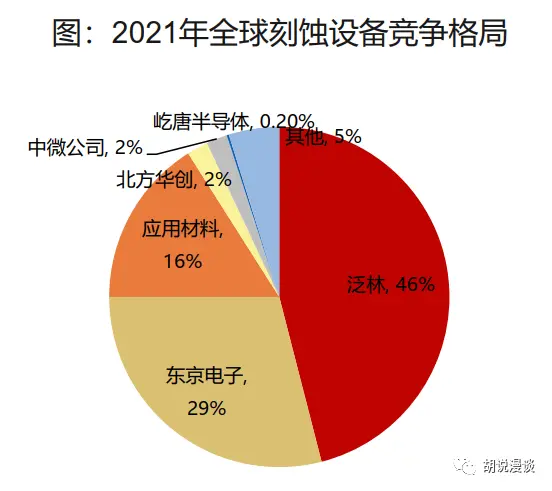
5、沉積設(shè)備:主要用來在硅片襯底上沉積薄膜沉,即在芯片納米級結(jié)構(gòu)中逐層堆疊薄膜形成電路結(jié)構(gòu),按薄膜種類可分為半導(dǎo)體、介質(zhì)、金屬/金屬化合物三大類;按工藝主要分為化學(xué)工藝和物理工藝。詳細(xì)的分類方法見下圖,接下來我們將進(jìn)行一一介紹。
薄膜按種類主要分為半導(dǎo)體、介質(zhì)、金屬/金屬化合物薄膜三大類,特點(diǎn)在于沉積材料與不同場景下應(yīng)用的復(fù)雜多樣,并且材料的進(jìn)步伴隨制程等的演變,推動薄膜沉積工藝/設(shè)備不斷研發(fā)。半導(dǎo)體薄膜的應(yīng)用范圍有限,主要用于制備源/漏極的溝道區(qū)、單晶外延層和MOS柵極等。介質(zhì)薄膜的應(yīng)用范圍最廣泛,主要用于前段的淺槽隔離、柵氧化層、側(cè)墻、阻擋層、金屬層前介質(zhì)層,后段的金屬層間介質(zhì)層、刻蝕停止層、阻擋層、抗反射層、鈍化層等,也可以用于硬掩膜。金屬/金屬化合物薄膜中的金屬薄膜主要用于金屬柵極、金屬層、焊盤,金屬化合物薄膜主要用于阻擋層、硬掩膜等。
薄膜的制備需要不同技術(shù)原理,因此導(dǎo)致薄膜沉積設(shè)備也需要不同技術(shù)原理,物理/化學(xué)等不同沉積方法相互補(bǔ)充薄膜沉積工藝主要分為物理和化學(xué)方法兩類,物理方法指利用熱蒸發(fā)或受到粒子轟擊時物質(zhì)表面原子的濺射等物理過程,實(shí)現(xiàn)物質(zhì)原子從源物質(zhì)到襯底材料表面的物質(zhì)轉(zhuǎn)移?;瘜W(xué)方法是指把含有構(gòu)成薄膜元素的氣態(tài)反應(yīng)劑或液態(tài)反應(yīng)劑的蒸汽,以合理的氣流引入工藝腔室,在襯底表面發(fā)生化學(xué)反應(yīng)并在襯底表面上沉積薄膜。
物理方法中的PVD(Physical Vapor Deposition,物理氣相沉積)主要用來沉積金屬及金屬化合物薄膜,最主要用于金屬互連籽晶層、阻擋層、硬掩膜、焊盤等。PVD分為蒸鍍(對金屬材料進(jìn)行加熱使之沸騰后蒸發(fā)并沉積)和濺射(帶電離子轟擊靶材表面將后者濺射出來射向襯底并沉積)兩大類,初期真空蒸鍍占據(jù)主流,后來由于不能蒸發(fā)一些難熔金屬和氧化物材料,因此逐步被濺射取代,同時由于薄膜性能要求等不斷升高,濺射PVD不斷改進(jìn)或迭代,目前應(yīng)用最廣泛的是磁控濺射PVD。
真空蒸鍍和濺射方法分別采用熱蒸發(fā)或受到粒子轟擊時物質(zhì)表面原子的濺射等物理過程,實(shí)現(xiàn)物質(zhì)原子從源物質(zhì)到襯底材料表面的物質(zhì)轉(zhuǎn)移,這一過程不涉及化學(xué)反應(yīng)。磁控PVD按照激勵源及濺射方式的不同也分為直流濺射DCPVD、射頻濺射RFPVD、磁控濺射PVD、離子化PVD(Ionized-PVD,為滿足高深寬比通孔和狹窄溝道的填充能力,而對磁控 DCPVD 做出的改進(jìn))等。普通真空蒸鍍和直流濺射方法只能沉積金屬或?qū)щ姳∧?,而不適用制備絕緣體薄膜,原因在于當(dāng)正離子轟擊絕緣體靶材表面時,會把動能傳遞給靶面,但正離子本身卻留在了靶材表面聚集,其產(chǎn)生的電場會對射向靶材表面的離子產(chǎn)生排斥,從而迫使濺射過程停止。一些高頻濺射,例如射頻濺射,也可以實(shí)現(xiàn)濺射絕緣材料。
物理方法中的旋涂顧名思義,在此不做贅述。另一種物理方法電鍍(Electrondeposition/Electroplating,ECD/ECP),其作用是將一層金屬的薄層鍍到另一層金屬上,主要用于后段工藝中對Cu等金屬導(dǎo)線和通孔的填充。ECD/ECP優(yōu)勢在于形成的薄膜具備更低的電阻率和更好的填充特性,但最大的缺陷在于高深寬比的溝槽填充很不理想,原因在于溝槽不同部位的電流密度不均勻。
化學(xué)方法中的CVD(Chemical Vapor Deposition,化學(xué)氣相沉積)指不同分壓的多種氣相狀態(tài)反應(yīng)物在一定溫度和氣壓下發(fā)生化學(xué)反應(yīng)來沉積薄膜。傳統(tǒng)CVD工藝中,沉積薄膜一般為氧化物、氮化物、碳化物等化合物或多晶硅,在特定領(lǐng)域的薄膜生長采用的外延(Epitaxy,EPI)技術(shù)廣義上也算 CVD 的一種。介質(zhì)薄膜所用的沉積材料種類和材料配比方式眾多,因此CVD設(shè)備細(xì)分品類大大多于PVD設(shè)備。
(1)APCVD(Atmospheric Pressure CVD,常壓化學(xué)氣相沉積)可用于制備單晶硅、多晶硅、二氧化硅、摻雜的 SiO2(PSG/BPSG)等簡單特性薄膜。APCVD是最早出現(xiàn)的CVD方法,反應(yīng)壓力為大氣壓,溫度大約400-800℃左右,優(yōu)勢在于反應(yīng)結(jié)構(gòu)簡單、沉積速率快,但缺點(diǎn)在于臺階覆蓋率差,因此一般僅適用于在微米制程中制備簡單的氧化硅等薄膜,用于層間介質(zhì)層和鈍化層等,在納米制程中逐步被其他工藝替代。
(2)LPCVD(Low Pressure CVD,低壓化學(xué)氣相沉積)是用于90nm以上的薄膜沉積主流工藝,用于制備SiO2和 PSG/BPSG(ILD、STI、側(cè)墻、柵氧化層等)、氮氧化硅(抗反射層等)、多晶硅、Si3N4(鈍化層、刻蝕停止層、硬掩膜等)、多晶硅(柵極)等薄膜。LPCVD的運(yùn)行氣壓在27~270Pa,氣壓較低,薄膜生長速率能更好控制,相較APCVD,其沉積的薄膜臺階覆蓋率等性能更好,缺點(diǎn)在于高溫反應(yīng),薄膜密度以及填孔能力相對有限。
(3)PECVD(Plasma Enhanced CVD,等離子增強(qiáng)化學(xué)氣相沉積)在制程進(jìn)步到90-28nm時成為主流,用于沉積介質(zhì)絕緣層和半導(dǎo)體材料。不同于APCVD/LPCVD使用熱能來激活和維持化學(xué)反應(yīng),PECVD特點(diǎn)是借助微波或射頻等使含有薄膜組成原子的氣體電離,在局部形成等離子體,而等離子體的化學(xué)活性很強(qiáng),容易發(fā)生反應(yīng),進(jìn)而在襯底上沉積出所需薄膜。PECVD反應(yīng)壓強(qiáng)與LPCVD相差不大,但等離子體能量反應(yīng)溫度較低(100~300℃),因此可在熔點(diǎn)更低的金屬互連層上沉積二氧化硅等薄膜,另外PECVD沉積速率更快、臺階覆蓋率更好,能夠沉積大多數(shù)主流的介質(zhì)薄膜、包括一些先進(jìn)的 low-k 材料、硬掩膜等。
(4)M-CVD(Metal-CVD,金屬CVD)用于沉積鎢及阻擋層等,特性是對孔隙和溝槽很好的臺階覆蓋率。M-CVD是指特含金屬前驅(qū)物的一類化學(xué)沉積技術(shù),最早用于沉積鎢,填充接觸孔隙及存儲器中的字線;隨著技術(shù)迭代,孔隙尺寸變小,鎢的阻擋層TiN的沉積方法從PVD轉(zhuǎn)為CVD,為了防止對鈦附著層的腐蝕及氯雜質(zhì),TiN的沉積不能使用TiCl4,因此一般轉(zhuǎn)而采用M-CVD沉積TiN。
(5)MOCVD(Metal-organic CVD,金屬有機(jī)化學(xué)氣相沉積)用于LED等領(lǐng)域的單晶材料制備。主要用于制備半導(dǎo)體光電子、微電子器件等領(lǐng)域的GaAs、GaN、ZnSe等單晶材料,用于化合物半導(dǎo)體LED、激光器、高頻電子器件和太陽能電池等領(lǐng)域。MOCVD 優(yōu)點(diǎn)為適用范圍廣、生長易于控制、重復(fù)性及連續(xù)性好。
(6)EPI指在單晶襯底上生長一層和襯底具有相同晶向的單晶薄膜材料。外延分為氣相外延和分子束外延兩種方法,硅片制造中為了改善器件性能通常在硅襯底上外延一層純度更高、缺陷密度和氧、碳含量均低的外延層;也可以在高摻雜硅襯底上生長外延層防止器件的閂鎖效應(yīng);外延層更先進(jìn)的應(yīng)用是通過在器件的源、漏和柵極區(qū)域沉積外延硅,減小接觸電阻,提高芯片運(yùn)行速度。
(7)溝槽填充類CVD主要包括 HDPCVD(High Density Plasma Enhanced CVD,高密度等離子體CVD )、SACVD(Sub-atmospheric CVD,次常壓CVD)、FCVD(Flowable CVD,流體CVD)等,是專門用于溝槽、孔洞處薄膜填充的設(shè)備。
HDPCVD是PECVD的一種特殊形式,同時發(fā)生薄膜沉積和濺射,能夠?qū)崿F(xiàn)對溝槽和孔隙自下而上的填充,沉積的薄膜致密度更高,雜質(zhì)含量更低。130-45nm制程中使用 HDPCVD填充金屬前介質(zhì)層、STI (淺溝槽隔離)等。SACVD設(shè)備在次常壓環(huán)境下反應(yīng),可以減小氣相化學(xué)反應(yīng)材料的分子自由程,通過臭氧在高溫環(huán)境下產(chǎn)生高活性的氧自由基,增加分子間的碰撞,實(shí)現(xiàn)優(yōu)越的填孔(Gap Fill)能力。45-14nm制程中使用SACVD實(shí)現(xiàn)對 STI、PMD(金屬前介質(zhì)層)等溝槽的填充或薄膜的沉積。FCVD是遠(yuǎn)程等離子體沉積技術(shù),反應(yīng)前驅(qū)物定向引入反應(yīng)腔室,對溝槽實(shí)現(xiàn)自下而上的填充,14nm 及以下制程中采用 FCVD完成對細(xì)小溝槽的無縫隙填充。
(8)ALD(Atomic Layer Deposition,原子層沉積)采用單原子層逐層生長,既可用于低k介質(zhì)也可用于金屬柵極/高k金屬化合物薄膜沉積。ALD通過脈沖波進(jìn)行單原子層膜逐層生長,將原子逐層沉積在襯底材料上,與CVD不同的是,CVD將不同反應(yīng)氣體同時導(dǎo)入腔室,ALD是讓不同材料的脈沖波在不同時間到達(dá)晶圓表面,兩種氣體周期性地進(jìn)行反應(yīng)。ALD可分為等離子ALD(PE-ALD)和熱ALD(Thermal-ALD),區(qū)別在于,PE-ALD使用離子體前驅(qū)物,反應(yīng)不需要加熱, 器件損傷小,主要用于沉積低k材料等介質(zhì);T- ALD需要加熱來發(fā)生反應(yīng),在高溫下進(jìn)行反應(yīng),沉積速率較快,薄膜致密性好,但是高溫可能損傷薄膜,主要用于沉積金屬柵極/高k金屬化合物薄膜。
ALD 特性在于臺階覆蓋率極高,在45nm以下節(jié)點(diǎn)每一代制程進(jìn)步均會擴(kuò)大ALD應(yīng)用場景。由于ALD逐層沉積原子,因此可以很好控制薄膜的厚度、成分和結(jié)構(gòu),同時臺階覆蓋率和溝槽填充均勻性極佳,特別是在一些對生長溫度及熱預(yù)算有限制,以及對薄膜質(zhì)量和臺階覆蓋率有較高要求的領(lǐng)域。另一方面ALD將物質(zhì)以單原子層的形式一層一層沉積在基底表面,每鍍膜一次/層為一個原子層,鍍膜10次/層約為1nm,因此其缺點(diǎn)在于沉積速率較慢,不適合大規(guī)模生產(chǎn),在45nm以上等成熟制程中相較LPCVD/PECVD工藝仍不具備成本或者沉積速率優(yōu)勢。
從市場規(guī)模來看,2021年全球薄膜沉積設(shè)備市場規(guī)模約190億美元,華經(jīng)產(chǎn)業(yè)研究院預(yù)計(jì)22年市場規(guī)模220億美元,同比增長16%。隨著制程縮小和存儲結(jié)構(gòu)3D化,薄膜沉積設(shè)備市場規(guī)模逐步擴(kuò)大。CVD覆蓋前段和后段工藝的大部分薄膜,是應(yīng)用最廣泛的薄膜沉積技術(shù),CVD占整體市場大約 75%,其中PECVD//LPCVD分別占整體市場33%/11%,SACVD及其他設(shè)備最主要用于填孔,典型應(yīng)用場景是淺槽隔離等,應(yīng)用更為有限,占整體市場約 6%;PVD最主要用于沉積金屬薄膜,而金屬薄膜用于后段工藝中的金屬層和前段的金屬柵極,應(yīng)用場景相較 CVD 有限,PVD 占整體市場比例大約 19%;ALD主要用于先進(jìn)制程工藝,占比約11%。
從競爭格局來看,PVD設(shè)備中的應(yīng)用材料是絕對龍頭,2021年全球市占率86%。CVD設(shè)備中應(yīng)用材料、泛林、東京電子三足鼎立,全球市占率分別為27%、 23%、 20%。ALD設(shè)備中先晶半導(dǎo)體(ASMI)、東京電子全球市占率分別為45%、29%。
6、離子注入機(jī):是離子注入工藝的核心裝備,主要用于光伏及集成電路制造中的摻雜(Doping)工藝,即將特定元素(B、P、As 等) 以離子形式加速到預(yù)定能量后注入至半導(dǎo)體材料(Si、Ge、SiC 等) 之中。摻雜的原因有很多,一般而言,硅單晶(最原始不含雜質(zhì))導(dǎo)電性能很差,只有當(dāng)硅中加入少量雜質(zhì),使其結(jié)構(gòu)和電導(dǎo)率發(fā)生改變時,硅才成為真正有用的半導(dǎo)體。例如硼和磷雜質(zhì)摻雜后成為硅器件的多數(shù)載流子,形成硅片的導(dǎo)電層,可以改變材料的性能,制成包括晶體管在內(nèi)的集成電路基本單元。此外摻雜還可以提高多晶硅柵電極的電導(dǎo)率。
在晶片制造中,有兩種方法可以引入雜質(zhì)元素,即熱擴(kuò)散(屬于熱處理設(shè)備)和離子注入,隨著特征尺寸的不斷減小,熱擴(kuò)散逐漸被取代,現(xiàn)代晶片制造幾乎所有摻雜工藝都是用離子注入實(shí)現(xiàn)的。離子注入機(jī)主要由氣體系統(tǒng)、電機(jī)系統(tǒng)、真空系統(tǒng)、控制系統(tǒng)、射線系統(tǒng)五大系統(tǒng)構(gòu)成,它具有兩個最基本的參數(shù):離子能量和注入劑量(單位面積注入離子個數(shù)) ,其中離子能量是決定摻雜深度的參數(shù), 而注入劑量是決定摻雜濃度的參數(shù)。離子注入機(jī)按照能量高低可以分為低能量/高能量,按照束流大小可以分為中低束流/大束流,按下游應(yīng)用可分為集成電路、光伏和AMOLED。
單就集成電路應(yīng)用來說,基于能量和劑量兩個基本參數(shù),應(yīng)用于集成電路制造的離子注入機(jī)主要分為三種機(jī)型,即大束流離子注入機(jī)、中束流離子注入機(jī)和高能離子注入機(jī),其中低能大束流離子注入機(jī)和高能離子注入機(jī)制造技術(shù)難度相對更高。
隨著先進(jìn)制程發(fā)展,對離子注入機(jī)的要求也更高。為適應(yīng)FinFET及3D NAND Flash需求,離子注入機(jī)需要具備更精確注入,更精確控制束斑形狀及注入劑量,以及高溫注入能力以降低注入導(dǎo)致晶格缺陷等。隨著芯片制程向14nm以下不斷縮小,低能大束流離子注入機(jī)逐漸成為主流。目前大束流離子注入占比約為 61%,中束流離子注入機(jī)與高能離子注入機(jī)分別占比 20%、18%。
從市場規(guī)模和競爭格局來看,2021 年全球、中國大陸離子注入機(jī)市場規(guī)模分別為30.8、8.9億美元。目前,全球離子注入機(jī)市場份額高度集中,主要被美國應(yīng)用材料、美國亞舍立科技、日本SMIT等廠商壟斷。根據(jù)尚普咨詢集團(tuán)數(shù)據(jù)顯示,應(yīng)用材料公司占全球集成電路離子注入機(jī)市場份額的55%以上,亞舍立科技占20%左右,SMIT占15%左右,其余廠商占10%左右。我國的凱世通、中科信已具備集成電路用離子注入機(jī)的研發(fā)和生產(chǎn)能力。
7、清洗設(shè)備:清洗環(huán)節(jié)的核心設(shè)備。清洗環(huán)節(jié)是影響芯片成品率、品質(zhì)及可靠性的重要因素之一,其步驟貫穿整個半導(dǎo)體制程, 用于去除半導(dǎo)體硅片制備、 晶圓制造和封裝測試每個步驟中可能存在的雜質(zhì)、 避免雜質(zhì)影響芯片良率和芯片產(chǎn)品的性能。隨著芯片制造工藝先進(jìn)制程的持續(xù)提升、線寬微縮,良率隨線寬縮小而下降,其中提高良率的方式之一就是增加清洗工藝的步驟,同時對清洗的質(zhì)量要求也在不斷提升。
清洗的具體應(yīng)用環(huán)節(jié)包括:硅片制造中,需要清洗拋光后的硅片,保證表面平整度和性能,提高良率;晶圓制造中,光刻、刻蝕、沉積等關(guān)鍵環(huán)節(jié)后需要進(jìn)行清洗,去除晶圓上的化學(xué)雜質(zhì),減少缺陷率;封裝環(huán)節(jié)中,根據(jù)封裝工藝進(jìn)行TSV清洗、UBM/RDL清洗等。我們在上一篇文章芯片產(chǎn)業(yè)鏈系列7半導(dǎo)體設(shè)備-硅片制造設(shè)備中已對清洗設(shè)備做了初步介紹,本篇文章我們將對其詳細(xì)介紹,在接下來的封裝設(shè)備介紹中我們將不再作過多贅述。
我們在芯片產(chǎn)業(yè)鏈系列3-超級長文解析芯片制造全流程一文中已經(jīng)知道,根據(jù)清洗介質(zhì)不同,半導(dǎo)體清洗技術(shù)主要分為濕法清洗和干法清洗兩種工藝路線。濕法清洗是主流的技術(shù)路線,可同時采用超聲波、加熱、真空等輔助技術(shù)手段,占芯片制造清洗步驟數(shù)量的90%以上。干法清洗雖然具有對不同薄膜有高選擇比的優(yōu)點(diǎn),但可清洗污染物比較單一,目前在28nm及以下技術(shù)節(jié)點(diǎn)的邏輯產(chǎn)品和存儲產(chǎn)品有應(yīng)用。具體的分別我們不再重復(fù)講述,總結(jié)為下表:
從清洗設(shè)備細(xì)分市場來看,根據(jù)清洗介質(zhì),可以分為干法清洗設(shè)備和濕法清洗設(shè)備。在實(shí)際生產(chǎn)過程中一般將兩者結(jié)合使用,根據(jù)清洗設(shè)備類型,可以分為單片清洗設(shè)備、槽式清洗設(shè)備、批式旋轉(zhuǎn)噴淋清洗設(shè)備、洗刷器等。在集成電路制造的先進(jìn)工藝中,單片清洗設(shè)備已取代槽式設(shè)備成為主流,主要由于單片清洗能夠在整個制造周期提供更好的工藝控制,改善單個晶圓和不同晶圓間的均勻性,提高產(chǎn)品良率;更大尺寸的晶圓和更先進(jìn)的工藝對于雜質(zhì)更敏感,槽式清洗出現(xiàn)交叉污染的概率更大。
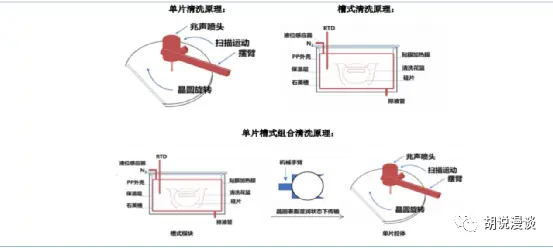
從市場規(guī)模來看,2021年全球半導(dǎo)體清洗設(shè)備市場規(guī)模達(dá)到39.18億美金,2021年我國半導(dǎo)體清洗設(shè)備市場規(guī)模為15億美金,占全球規(guī)模的39.28%。清洗設(shè)備各細(xì)分品類的價(jià)值量來看,單片清洗設(shè)備、槽式清洗設(shè)備、批式旋轉(zhuǎn)噴淋清洗設(shè)備、洗刷器等,占比分別為 74.6%、 18.1%、 0.4%、 6.8%。
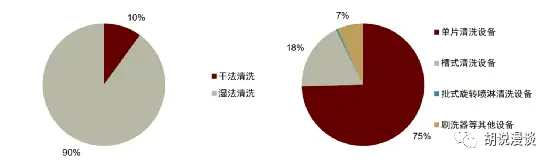
從競爭格局來看,2021年全球半導(dǎo)體清洗設(shè)備CR4達(dá)93%。日本DNS、TEL占據(jù)龍一龍二,市占率分別為40%、25%;韓國細(xì)美事和美國泛林分別占據(jù)16%、 12%。國產(chǎn)清洗設(shè)備公司主要有盛美上海、北方華創(chuàng)、至純科技和芯源微。盛美憑借獨(dú)創(chuàng)兆聲波清洗技術(shù)市占率最高,2021年全球市占率3.1%。

8、CMP設(shè)備:CMP環(huán)節(jié)的核心設(shè)備,使用化學(xué)腐蝕及機(jī)械力對加工過程中的硅晶圓或其它襯底材料進(jìn)行平坦化處理。CMP設(shè)備包括拋光、清洗、傳送三大模塊,其作業(yè)過程中,拋光頭將晶圓待拋光面壓抵在粗糙的拋光墊上,借助拋光液腐蝕、微粒摩擦、拋光墊摩擦等耦合實(shí)現(xiàn)全局平坦化,使晶圓拋光后表面達(dá)到超高平整度且表面粗糙度小于 0.5nm,再進(jìn)行清洗,在不破壞晶圓表面極限化微縮對的特征結(jié)構(gòu)的情況下,降低其晶圓顆粒物數(shù)量。
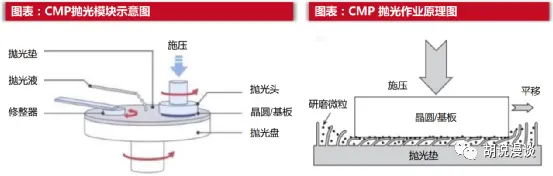
目前的集成電路元件普遍采用多層立體布線,因此集成電路制造的前道工藝環(huán)節(jié)要進(jìn)行多次循環(huán)。在此過程中, CMP技術(shù)是集成電路(芯片)制造過程中實(shí)現(xiàn)晶圓表面平坦化的關(guān)鍵工藝,是集成電路制造中推進(jìn)制程技術(shù)節(jié)點(diǎn)升級的重要環(huán)節(jié)。此外與清洗工藝一樣,CMP工藝也貫穿整個半導(dǎo)體制造產(chǎn)業(yè)鏈,即硅片制造、晶圓加工、封裝測試三大領(lǐng)域均有CMP的應(yīng)用場景。
按硅片尺寸分,CMP設(shè)備有適用于12英寸和8英寸兩類,12 英寸CMP設(shè)備是業(yè)界公認(rèn)的衡量一個廠家研發(fā)技術(shù)水平的標(biāo)桿產(chǎn)品。目前90nm以下工藝的高端市場普遍采用12英寸硅片進(jìn)行加工,12英寸與8英寸相比直徑增長50%、面積擴(kuò)大125%,對拋光精度的要求更高,因此需要使用更先進(jìn)的拋光頭超精密分區(qū)壓力控制技術(shù)和終點(diǎn)檢測技術(shù)。
CMP市場主要分為設(shè)備和耗材(拋光液、拋光墊),其中CMP耗材占接近68%,CMP設(shè)備為32%。從市場規(guī)模來看,根據(jù)SEMI數(shù)據(jù),2021年全球CMP設(shè)備市場規(guī)模迅速回升至27.83億美元;2022年,全球CMP設(shè)備市場規(guī)模為27.78億美元,市場規(guī)模保持穩(wěn)定。
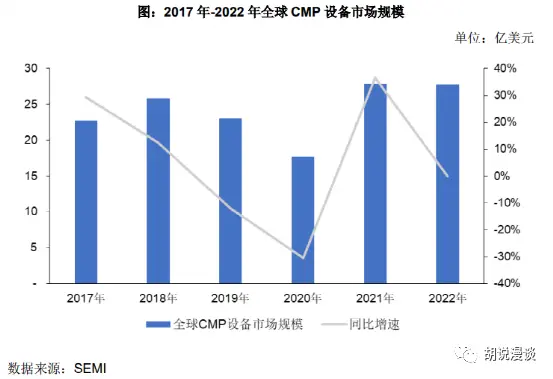
從競爭格局來看,全球CMP設(shè)備市場主要由美國應(yīng)用材料和日本荏原占據(jù),處于高度壟斷狀態(tài)。根據(jù)Gartner數(shù)據(jù),上述兩家制造商的CMP設(shè)備全球市場占有率超過90%,尤其在14nm以下先進(jìn)制程工藝產(chǎn)線上使用的CMP設(shè)備主要由美國應(yīng)用材料和日本荏原兩家國際巨頭提供。國內(nèi)從事CMP設(shè)備業(yè)務(wù)的主要企業(yè)有公司及華海清科。
9、測試設(shè)備:半導(dǎo)體測試環(huán)節(jié)的核心設(shè)備。實(shí)際生產(chǎn)過程中,缺陷貫穿始終,如果未及時修正將會導(dǎo)致半導(dǎo)體生產(chǎn)的最終失效,發(fā)現(xiàn)及修正缺陷所需要的測試也成為貫穿于集成電路設(shè)計(jì)、制造、生產(chǎn)中的、保證芯片質(zhì)量的重要環(huán)節(jié)。芯片從設(shè)計(jì)到失效整個壽命中所經(jīng)歷的測試主要有設(shè)計(jì)驗(yàn)證、工藝監(jiān)控測試、晶圓測試、最終測試、可靠性測試、用戶測試,其中前四個發(fā)生在制造過程中,相應(yīng)的所需要的測試設(shè)備包括過程工藝監(jiān)測過程中的光學(xué)設(shè)備等、晶圓中測中的探針臺等以及最終檢測過程中的分選機(jī)、測試機(jī)等。
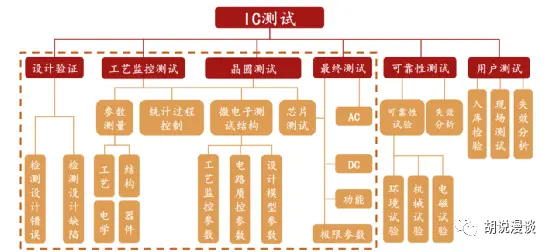
設(shè)計(jì)驗(yàn)證在量產(chǎn)前進(jìn)行,終測在芯片封裝后進(jìn)行,所有測試目的是保證芯片符合規(guī)格,盡量避免損失升級。設(shè)計(jì)驗(yàn)證主要檢測芯片樣品功能設(shè)計(jì),只有通過的產(chǎn)品型號才會開始進(jìn)入量產(chǎn),由于其發(fā)生在芯片制造最早環(huán)節(jié),性價(jià)比相對最高,可為芯片量產(chǎn)指明方向。設(shè)計(jì)驗(yàn)證過程包括所有芯片制造流程,所需測試設(shè)備也包含了全部半導(dǎo)體測試設(shè)備。在線參數(shù)測試主要指的是晶圓制造加工過程中的過程工藝控制設(shè)備,即我們通常所說的量/檢測設(shè)備。CP測試中的設(shè)備主要進(jìn)行電性測試,是在封裝前的最后一道防線,通過測試的晶圓將進(jìn)入封裝切割環(huán)節(jié),其標(biāo)準(zhǔn)直接影響芯片最終測試環(huán)節(jié)的良品率。終測是對封裝后的芯片進(jìn)行功能和電參數(shù)性能測試,是芯片進(jìn)入系統(tǒng)前的最后檢測。如果在先進(jìn)封裝中還有一步中道檢測,主要對RDL、Bumping、硅通孔進(jìn)行檢測。
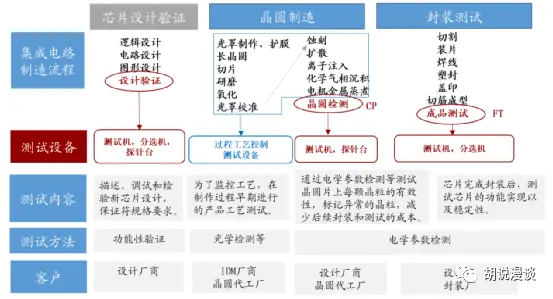
本文我們主要介紹前道制造過程中所用到的量/檢測設(shè)備。雖然嚴(yán)格意義上來說CP測試屬于封裝之前的晶圓加工環(huán)節(jié),但一來部分機(jī)構(gòu)統(tǒng)計(jì)前道設(shè)備行業(yè)數(shù)據(jù)時主要集中于量/檢測設(shè)備,二來CP測試設(shè)備用到的測試機(jī)與FT測試中用到的一樣,實(shí)際上將CP測試劃歸到后道測試之中更為方便。由于篇幅所限,我們將在下一篇文章中進(jìn)行介紹。需要注意的是,我們通常所說的晶圓檢測包括硅片測試及晶圓中測CP測試,硅片測試我們在上一篇文章中《硅片制造設(shè)備》已經(jīng)進(jìn)行了介紹,本文不再贅述。
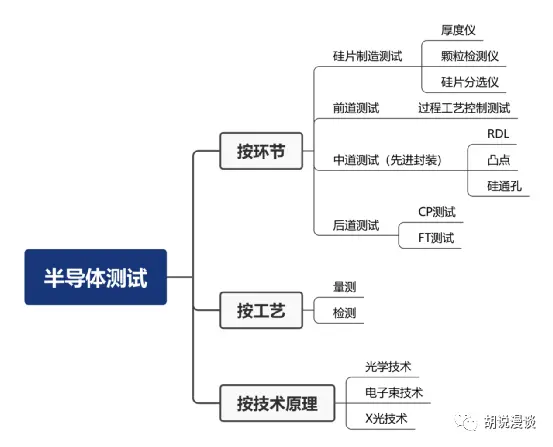
量/檢測是半導(dǎo)體制造重要的質(zhì)量檢查工藝,涉及膜厚、折射率、膜應(yīng)力等參數(shù)測量,以及各類表面缺陷檢測等,對硅片廠/晶圓廠保障產(chǎn)品良率、產(chǎn)品一致性、降低成本等至關(guān)重要。
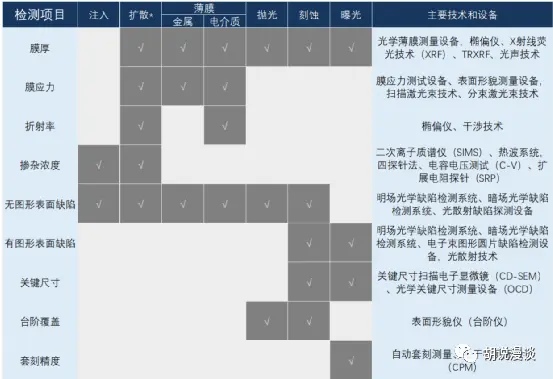
根據(jù)應(yīng)用場景的不同,量/檢測設(shè)備主要分為量測、檢測兩大類。檢測設(shè)備主要用于檢測晶圓結(jié)構(gòu)中是否出現(xiàn)異質(zhì)情況,如顆粒污染、表面劃傷、開短路等特征性結(jié)構(gòu)缺陷;量測設(shè)備指對被觀測的晶圓電路上的結(jié)構(gòu)尺寸和材料特性做出量化描述,如薄膜厚度、關(guān)鍵尺寸、刻蝕深度、表面形貌等物理參數(shù)的測量。
按照技術(shù)原理劃分,量/檢測設(shè)備可分為光學(xué)、電子束、 X光三大類。光學(xué)技術(shù)對晶圓破壞性小,同時具備批量、快速檢測的優(yōu)點(diǎn),廣泛應(yīng)用于晶圓表面雜質(zhì)顆粒、圖案缺陷等檢測,以及膜厚、關(guān)鍵尺寸、套刻精度、表面形貌等測量;電子束技術(shù)的精度高于光學(xué)技術(shù),但是速度較慢,適用于部分核心工藝的抽檢;X光技術(shù)穿透力強(qiáng)、無損探測,適用于超薄薄膜測量、特定金屬成分檢測等少數(shù)特殊場景。
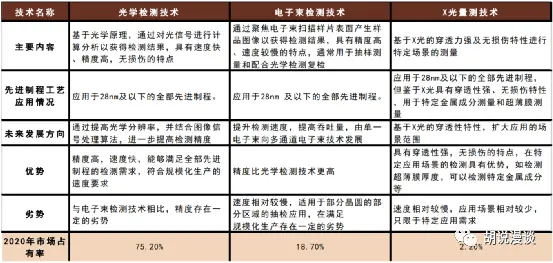
從市場規(guī)模來看,量/檢測設(shè)備在半導(dǎo)體設(shè)備中價(jià)值量占比較高( 約11%), 2021年全球半導(dǎo)體檢測設(shè)備市場空間約110多億美元,僅次于三大核心設(shè)備(薄膜沉積、光刻和刻蝕),排名第四,明顯高于清洗、涂膠顯影、CMP等環(huán)節(jié)。細(xì)分設(shè)備類別來看,按應(yīng)用場景看,檢測設(shè)備占比高達(dá)63%,按技術(shù)原理看,光學(xué)類占比高達(dá)75%。進(jìn)一步細(xì)分來看,2020年各類缺陷檢測類設(shè)備占據(jù)量/檢測設(shè)備近六成市場份額,其中納米圖形晶圓缺陷檢測設(shè)備、掩模版缺陷檢測設(shè)備、無圖形缺陷檢測設(shè)備、圖形缺陷檢測設(shè)備價(jià)值量占比分別達(dá)到24.7%、11.3%、9.7%和6.3%。此外,關(guān)鍵尺寸量測設(shè)備也是前道量/檢測設(shè)備重要組成部分, 2020年價(jià)值量占比達(dá)到10.2%。
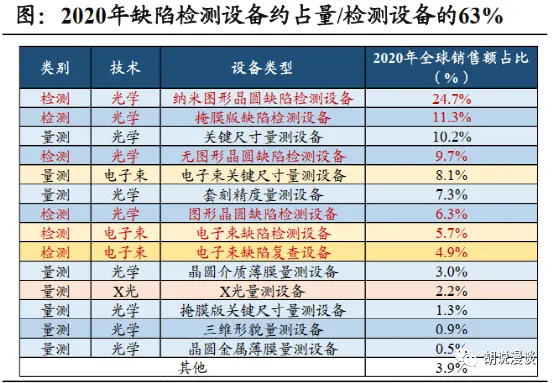
從競爭格局來看,量測設(shè)備市場呈現(xiàn)出高度壟斷的格局,根據(jù)Gartner數(shù)據(jù)2021年行業(yè)前5名分別為KLA、AMAT、日立高新(Hitachi High-Tech)、創(chuàng)新科技(Onto Innovation)、新星測量儀器(Nova Measuring),行業(yè)TOP3占據(jù)75%的市場份額。美國的KLA牢牢占據(jù)行業(yè)的龍頭地位,市場占有率超過行業(yè)第二的四倍。KLA 長期在半導(dǎo)體制造中過程控制業(yè)務(wù)領(lǐng)域份額超過50%,2021年以54%位列第一。尤其是在晶圓形貌檢測、無圖形晶圓檢測、有圖形晶圓檢測領(lǐng)域,KLA全球市場份額更是分別高達(dá)85%、78%、72%。國內(nèi)主要企業(yè)為中科飛測、上海精測、上海睿勵等。
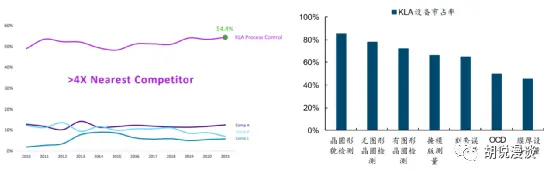
以上我們對半導(dǎo)體晶圓加工設(shè)備分別進(jìn)行了系統(tǒng)梳理,需要注意的是也可以對這些設(shè)備按五大工藝分區(qū)進(jìn)行分類。具體地,光刻機(jī)和涂膠顯影設(shè)備屬于黃光區(qū),刻蝕機(jī)屬于刻蝕區(qū),薄膜設(shè)備屬于真空區(qū),離子注入機(jī)和熱處理設(shè)備屬于擴(kuò)散區(qū),CMP、清洗及量檢測設(shè)備屬于輔助區(qū)。下周我們繼續(xù)介紹半導(dǎo)體制造中的封測設(shè)備。