化工行業(yè) mes 智能生產(chǎn)制造執(zhí)行系統(tǒng)解決方案
在面對復雜多變的市場環(huán)境以及節(jié)能環(huán)保的主題之下,化工行業(yè)面臨著越來越嚴峻的生存環(huán)境,因此轉(zhuǎn)型升級成為了化工行業(yè)的必經(jīng)之路?;ば袠I(yè)具有生產(chǎn)連續(xù)性強、工藝參數(shù)變化多、物料變化復雜、質(zhì)量管理復雜、設(shè)備管理繁雜等特點,那么化工企業(yè)該如何導入 MES 系統(tǒng)呢?
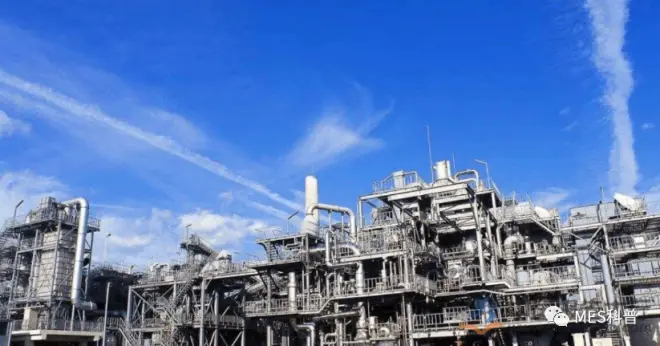
化工行業(yè)生產(chǎn)特點
從整體上來說,化工生產(chǎn)過程是對生產(chǎn)原料伴有化學、物理、相變等反應、變化過程的連續(xù)加工。和離散制造業(yè)相比,化工企業(yè)具有以下特殊性:
1.生產(chǎn)連續(xù)性強:由于化工產(chǎn)品生產(chǎn)的連續(xù)性,生產(chǎn)裝置、生產(chǎn)流程的連續(xù)性很強,因為生產(chǎn)是連續(xù)的,一個環(huán)節(jié)發(fā)生問題就會阻塞整個流程,帶來連鎖反應,因此,化工 MES 系統(tǒng)要解決的問題就是,及時快速地反應生產(chǎn)狀況和生產(chǎn)變化,及時對發(fā)生的問題做出快速反應,避免無價值的生產(chǎn)。
2.工藝參數(shù)變化多 :成品收率是生產(chǎn)計劃密切關(guān)注的。而影響化學反應的因素很多,設(shè)備、原料、操作都會影響產(chǎn)成品的收率,這些影響主要表現(xiàn)為工藝參數(shù)的變化,化工 MES 系統(tǒng)解決方案,需要提升企業(yè)的工藝控制能力,保證產(chǎn)品生產(chǎn)正常、順利推進,從而保證產(chǎn)品的效率與質(zhì)量。
3.物料變化復雜:生產(chǎn)加工高度的連續(xù)性,各個工序之間通過物料流和能量緊密的聯(lián)系起來。一旦生產(chǎn)計劃改變,整個生產(chǎn)流程的各個環(huán)節(jié)的生產(chǎn)狀況都會隨之變化,因此實施化工 MES 解決方案需要銅鼓 MES 系統(tǒng)提升對突、臨時生產(chǎn)查單的適應性。化工材料會隨時間的變化而產(chǎn)生變化,可能變壞或變好,或完全變成另外一種物料;有些原料取自自然界,不同地點、批次的原料,其物理、化學性能會有差異。所以化工 MES 系統(tǒng),需要能夠標識并管理物料實施變化狀態(tài)和情況。
4.質(zhì)量管理復雜:化工生產(chǎn)中的質(zhì)檢計量不僅有質(zhì)量管理的作用,同時也是一種檢測化工產(chǎn)品中生成物含量的比例一種手段,因此也是一種成本計算手段。因此化工、MES 系統(tǒng)需要支持質(zhì)量,物流.成本的統(tǒng)一計量管理。
5.設(shè)備管理繁雜:化工生產(chǎn)流程長,設(shè)備多而雜,因此生產(chǎn)開停車時,準備工作多而復雜,設(shè)備大修一般一年一次,全廠要停車,設(shè)備管理繁雜。
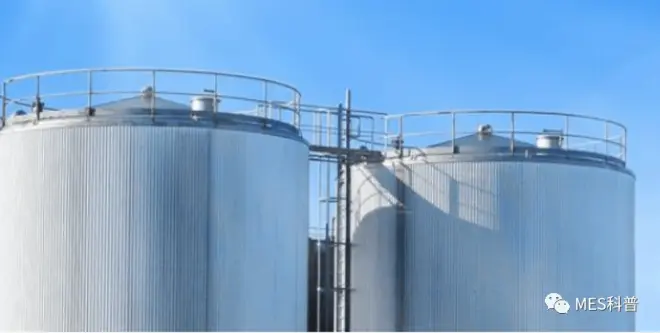
化工生產(chǎn)管理現(xiàn)狀
實施化工 MES 解決方案,是化工行業(yè)信息化建設(shè)中一個非常明顯的趨勢。通過實施化工 MES系統(tǒng),可以從企業(yè)整體出發(fā)逐層完成綜合信息管理、車間控制、裝置協(xié)調(diào)聯(lián)合控制、輔助裝置與設(shè)備的控制、能源監(jiān)測與計量控制等等,實現(xiàn)綜合管控一體化。但要實現(xiàn)這一目標,化工 MES 系統(tǒng)需要解決化工生產(chǎn)管理現(xiàn)狀中以下難題:
1.數(shù)據(jù)收集困難,除了 DCS 顯示數(shù)據(jù)外,現(xiàn)場流量計、配電間電表、磅秤等分散在現(xiàn)場,每天人工抄寫、傳送這些數(shù)據(jù)很繁瑣;
2.日常報表有日報、旬報、月報、生產(chǎn)簡況報告等,大部分報表仍然采用人丅統(tǒng)計,手段落后。工作量大、準確度難以保證。
3.調(diào)度員通訊手段落后,一般都以電話調(diào)度為主,調(diào)度員不了解現(xiàn)場設(shè)備運行狀況,需要通過電話問接了解,因此難以做到及時準確調(diào)度指揮。
4.質(zhì)量檢驗種類多,信息數(shù)據(jù)量大,生產(chǎn)工藝參數(shù)和質(zhì)量分析數(shù)值依靠人工抄表,效率低,占用定員多;化驗報告需要經(jīng)常送多個部門,化驗員大部分時間忙于送化驗報告,不便干生產(chǎn)過程分析和工藝技術(shù)管理。
5.一些信息化程度較高的企業(yè)已經(jīng)具有了相對完整的 PCS、ERP 系統(tǒng)。但市場定單無法準確分解轉(zhuǎn)化為生產(chǎn)計劃直接下達到生產(chǎn)調(diào)度,而 ERP 層在生產(chǎn)控制數(shù)據(jù)的獲取方面同樣存在巨大障礙,傳統(tǒng)的手工錄入方式不能克服信息滯后、數(shù)據(jù)失真等問題。
化工 MES 系統(tǒng)實現(xiàn)目標
1、生產(chǎn)數(shù)據(jù)整合利用,能夠隨時為管理人員提供自己所需要的信息,
2、建立一個規(guī)范完整的生產(chǎn)管理流程,提高生產(chǎn)管理的工作效率;
3、建立一個高效的生產(chǎn)管理工作平臺,讓各個級別管理人員能夠及時的獲得所關(guān)心的信息,只會或者執(zhí)行其他工作;
4、加強生產(chǎn)管理和過程監(jiān)控,能夠讓生產(chǎn)管理工作可以追溯考察,這樣可以追查他的最新情況。
5、推行一個新的生產(chǎn)管理理念,幫助企業(yè)建立一個信息化生產(chǎn)管理方法,提高企業(yè)的生產(chǎn)管理水平
化工行業(yè) MES 系統(tǒng)需要用信息化方式,實現(xiàn)信息化高效數(shù)據(jù)采集、統(tǒng)計、分析和報表生成,及時對生產(chǎn)現(xiàn)場的異常變化作出反應,通過全程監(jiān)控支持產(chǎn)品生產(chǎn)的全程追溯管理,實現(xiàn)全面的生產(chǎn)管控。
化工行業(yè) MES 系統(tǒng)解決方案
MES 系統(tǒng)在化工行業(yè)的信息化建設(shè)中地位與效益,在越來越多的化工 MES 系統(tǒng)成功案例中得以證明?;ば袠I(yè)的生產(chǎn)特點包括了:生產(chǎn)連續(xù)性強、工藝參數(shù)變化多、物料變化復雜、質(zhì)量管理復雜設(shè)備管理繁雜等,基于化工行業(yè)的特性來定制 MES 系統(tǒng)解決方案。
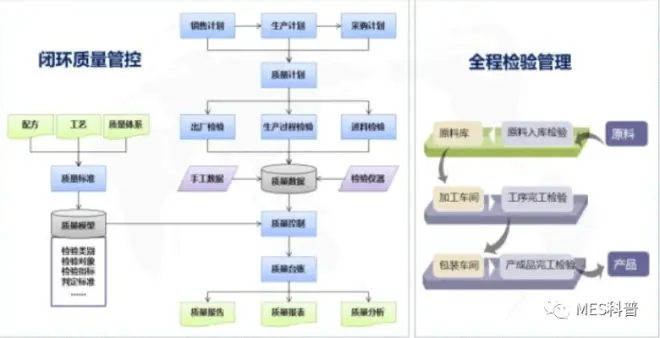
品質(zhì)追溯,源頭溯源
通過 MES 可視化建模,建立產(chǎn)品工藝標準,質(zhì)量標準,結(jié)合生產(chǎn)實時監(jiān)控,對比質(zhì)量指標,通過 SPC 分析,過程預測和預警,提前預測工藝或質(zhì)量事件,調(diào)整工藝操作,預防質(zhì)量事故的發(fā)生。建立質(zhì)量管控體系,植入電子批記錄,將質(zhì)量管理從報檢單,檢驗單,質(zhì)量異常改善單,不合格品處理單,報廢申請單,返工申請單等進行流程管控,并按照產(chǎn)品進行過程關(guān)聯(lián),追溯產(chǎn)品質(zhì)量的全過程,提升產(chǎn)品合格率。
將國家或公司質(zhì)量檢驗標準導入系統(tǒng),方便質(zhì)檢人員在作業(yè)時自動推送抽檢方式,化驗方式和分析等。
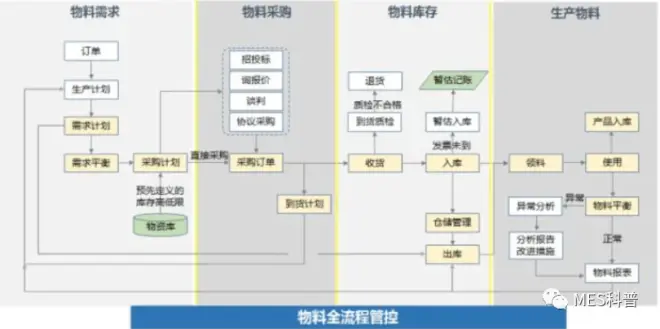
實施監(jiān)控,過程管理
MES 系統(tǒng)將幫助工廠車間建立一個服務干整個生產(chǎn)車間的生產(chǎn)實時監(jiān)控系統(tǒng),實現(xiàn)車間對各生產(chǎn)工序的集約化、實時化、精細化、專業(yè)化管理,推動生產(chǎn)技術(shù)制度體系向標準化、信息化、流程化持續(xù)改進。
將車間各獨立和分散的監(jiān)控、監(jiān)測系統(tǒng)整合到統(tǒng)一的數(shù)據(jù)平臺,建立龐大的基于設(shè)備和過程的實時數(shù)據(jù)倉庫,組建關(guān)鍵設(shè)備模型,將海量離散數(shù)據(jù)結(jié)構(gòu)化,構(gòu)筑數(shù)字化車間生產(chǎn)中關(guān)鍵的實時動態(tài)模型平臺,并利用設(shè)備編碼將設(shè)備動態(tài)屬性向業(yè)務層開放,允許其他非運行的專業(yè)技術(shù)人員,利用實時平臺,共同參與對設(shè)備以及生產(chǎn)過程的實時數(shù)據(jù)的分析、處理和應用。開發(fā)基于實時信息的應用模塊,通過對實時和歷史數(shù)據(jù)的處理、篩選、挖掘,使生產(chǎn)過程保持最佳的效率。
生產(chǎn)實時監(jiān)控將實現(xiàn)車間對生產(chǎn)指標信息的共享,滿足集中過程監(jiān)視和重大異常事件的管控和追溯,通過實時對標管理,直觀統(tǒng)計分析生產(chǎn)、運行現(xiàn)狀,改善指標偏差,同時,幫助生產(chǎn)中心打造合“生產(chǎn)數(shù)據(jù)+專業(yè)知識+生產(chǎn)運行經(jīng)驗”的遠程分析指揮中心,并且能對生產(chǎn)過程事件進行監(jiān)視(包括歷史數(shù)據(jù)),生產(chǎn)過程運行管理和統(tǒng)計報表的自動生成,輔助生產(chǎn)人員對全車間生產(chǎn)過程進行優(yōu)化提供指導和支撐。
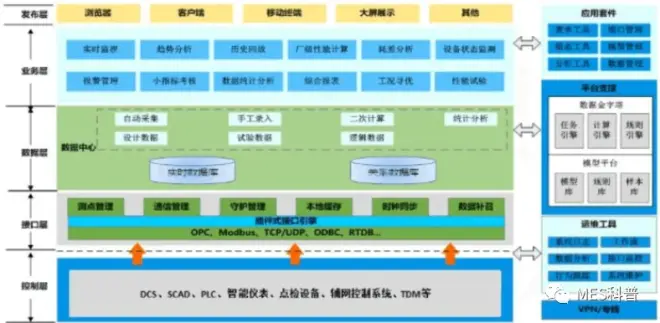
計劃排產(chǎn),資源協(xié)調(diào)
MES 系統(tǒng)提供全方位的生產(chǎn)計劃排程,利用先進的信息科技及規(guī)劃技術(shù),例如遺傳算法、限制理論、運籌學、生產(chǎn)仿真及限制條件滿足技術(shù)等,在考慮企業(yè)資源(主要為物料與設(shè)備產(chǎn)能)限制條件與生產(chǎn)現(xiàn)場的控制與派工法則下,規(guī)劃可行的物料需求計劃與生產(chǎn)排程計劃,以滿足顧客需求及面對競爭激烈的市場需求。
讓生產(chǎn)決策人員快速結(jié)合生產(chǎn)信息(如訂單、制程、存貨、BOM 與產(chǎn)能限制等),作出平衡企業(yè)利益與顧客權(quán)益的最佳規(guī)劃和決策,并在第一時間調(diào)度各類資源,包括人員、物料、生產(chǎn)設(shè)備等,提高各業(yè)務部門的協(xié)作配合能力,提高生產(chǎn)效率。